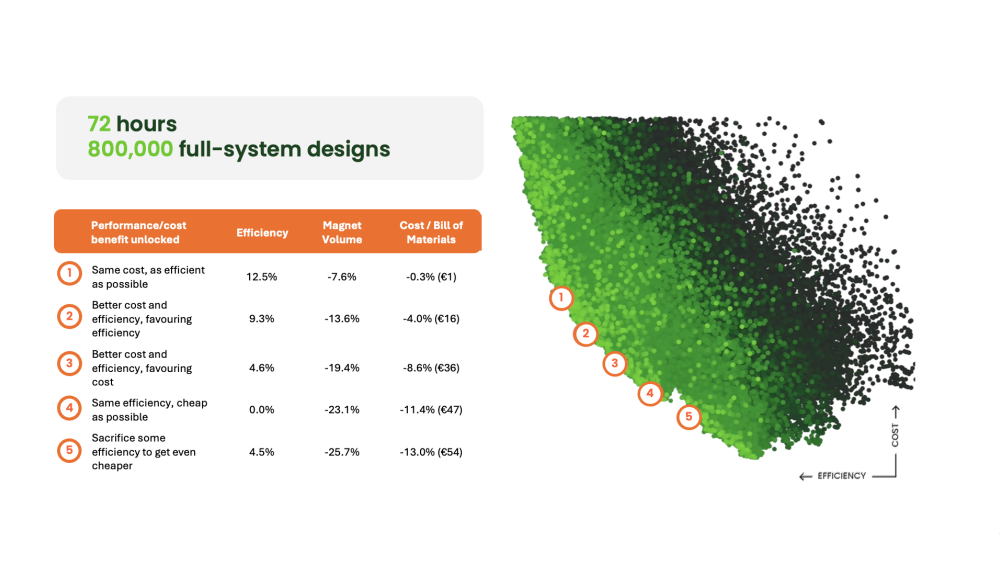
The evolving role of machine learning in powertrain engineering
The rapid rise of vehicle electrification is shaking the foundations of the automotive industry, forcing traditional OEMs to rethink not only their vehicle designs, but also the capabilities of their engineering teams. As global supply chains strain under the demand for critical raw materials, especially rare earth elements, developing sustainable and profitable products has never been more challenging.
At first glance, the surge of AI and deeptech might seem like yet another disruption that manufacturers must scramble to address. But at Monumo, we see it differently. We believe the real opportunity lies in harnessing the power of deeptech and advanced computing to become a driving force behind electrification. By embracing these technologies, OEMs can transform their approach to:
- Engineer superior EV powertrains with lower costs, longer ranges, and higher performance
- Accelerate time-to-market
- Build resilience against supply chain disruptions and reduce dependence on rare materials
- Empower their existing workforce to focus on more customer-centric innovations
Rather than just another challenge, deeptech represents a key differentiator in the race to electrification.
The Disruptive Shift
The transition from internal combustion engines (ICE) to electric vehicles (EV) has not only revolutionised propulsion systems, but also disrupted the once-stable process of powertrain development. Gasoline and diesel engines reached a level of maturity that brought stability and predictability to product development. In contrast, EV powertrain designers are navigating a rapidly evolving landscape, where technology is advancing at an unprecedented pace. Crafting a sound product technology strategy in this environment is increasingly challenging but crucial. The ability to anticipate and adapt to these changes can mean the difference between success and failure in the highly competitive EV sector.
Traditional Approaches: Limitations of Conventional Product Development
In traditional product development, engineers typically design to meet specifications derived from vehicle platform targets. However, time pressures often limit early collaboration between different sub-system teams, resulting in system-level decisions and trade-offs being made without fully exploring the impact of alternative architectural options. This lack of early-stage collaboration means that genuine system-level optimisation is rarely achieved.
During the concept phase of powertrain development, many definitive decisions are made that lock significant engineering resources into evolving and maturing a design. Once the powertrain architecture is set, reversing or refining it becomes too risky, time-consuming, and expensive. For instance, choosing axle gear ratios significantly influences the torque and speed demands on the electric motor; key factors in the power density and overall system performance. Evaluating these competing factors in detail is often too time-consuming for designers working within compressed development timelines.
The number of design iterations is typically limited by the time required to run complex multi-physics simulations, which often involve different software environments and specialists. In addition, manufacturers are pressured to meet aggressive prototype and validation schedules, leaving little room for detailed exploration of design alternatives.
As a result, OEMs frequently adapt existing reference designs from previous programs to ensure faster, safer routes to production and to mitigate technical risks. While this approach reduces the chances of missing deadlines, it also hinders the ability to fully optimise designs for new applications. Once key architectural decisions are made, no amount of downstream optimisation can change them, leaving OEMs with sunk costs and uncertainty about whether their product will remain competitive by the time it hits the market—especially when competing with industry leaders like Tesla and BYD.
Reversing the Traditional Process: From Requirements to Designs vs. Geometry to Performance
Monumo’s experienced engineering, simulation, and machine learning teams are continually advancing the capability to automate the evaluation of a wide range of design concepts at a system level—including motor, inverter, control strategy, and gearbox—right from the early stages of design.
At the core of this transformation is Monumo’s groundbreaking technology, known as the Anser™ engine, which allows exploration of the design parameter space with unprecedented freedom. Unlike conventional methodologies, Anser offers far greater coverage (of the potential design space), giving designers a much clearer picture of the key levers that drive optimal powertrain architectures. To illustrate the scale of this capability, Anser can run hundreds of thousands of simulations in a single day, offering unmatched insights.
Already, Anser can generate detailed and mature design concepts within days, once key requirements and design criteria are defined. However, this is only a stepping stone in Monumo’s broader vision.
Leveraging Machine Learning for Design Optimisation
The enormous volume of simulation data produced by Anser is ideal for training sophisticated machine learning algorithms, which we call "engineering models." These models can predict the performance of a wide range of powertrain design possibilities. Once trained on a specific operational or parametric domain, these models could soon be queried by engineers using algorithms similar to search engines, where simple input design rules yield refined solutions.
When Monumo reaches this milestone, it will fundamentally change how powertrain designs are conceived. The Anser engine will be able to propose alternative parametric design solutions based on performance requirements, with simulations backing each proposed concept. Because of the depth embedded in the training data, each query could generate highly refined designs in a few days —a process that currently takes multi-disciplinary teams, weeks or even months to complete.
Transforming the Speed and Depth of Design
Monumo’s process not only enables partners to create industry-leading designs but also reduces time-to-market significantly. In the future, we estimate that up to 80% of design time can be removed from the A-phase concept design stage. This timesaving also allows a much broader range of system solutions to be evaluated in detail.
As more elements of the overall powertrain system are co-optimised within a single, integrated process, the efficiency gains grow, unlocking significant performance improvements across the vehicle.
Shifting Engineering Focus
Monumo’s technology has the potential to revolutionise the way engineering teams operate. Instead of spending valuable time on basic iterations, engineers can now shift their focus toward evaluating how design criteria impact the final product, the customer experience, and key vehicle attributes like cost, performance, and driving characteristics. For example, engineers can explore how changes to acceleration targets or top speeds affect overall product costs.
This approach also addresses a critical challenge many established OEMs face today: how to utilise the skills of their existing engineering workforce, which was honed through internal combustion engine (ICE) development. Working with Monumo as a partner, powertrain engineers can apply their experience in developing next-generation EV concept designs without requiring deep knowledge in specialised fields such as electromagnetics.
Anser: Unlocking the Future of Powertrain Design
The Anser engine offers far more than just faster and more optimised designs. It will provide engineering teams with a clear, detailed view of the downstream effects of their design decisions from the earliest stages. This transparency enables more informed choices regarding system-level costs and performance, enhancing competitiveness.
Looking ahead, pre-trained engineering models based on Monumo’s technology will evolve to encompass a wider array of motor and drive system information across a broader operational domain. As these models become increasingly generalised, they will start to align with Monumo’s vision of the Targeted Engineering Models (TEMs)This evolution will allow Anser to address a broader spectrum of system elements that OEMs care about, covering multi-motor and multi-platform products. Consequently, manufacturers will be empowered to optimise performance across their entire product range, while effectively tackling complex supply chain challenges.
Conclusion: The Future of Electrification
As electrification continues to disrupt the global automotive sector, established OEMs are under immense pressure to stay competitive. Monumo believes that deeptech, exemplified by technologies like Anser, will be the key differentiator between those who merely survive and those who thrive in the fast-evolving landscape of automotive innovation.